Research news
The Sussex researchers who used international collaboration and 3D printing to stem PPE shortages in Nigeria
By: Stephanie Allen
Last updated: Monday, 27 June 2022
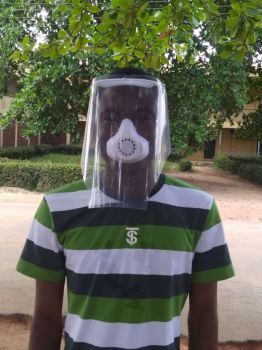
Researchers at the University of Sussex and their partners in Nigeria used open-source designs and 3D printing to reduce personal protective equipment (PPE) shortages for a community in Nigeria during the Covid-19 pandemic – tells a recently published academic paper.
In their paper in PLOS Biology, Dr Andre Maia Chagas from the University of Sussex, and Dr. Royhaan Folarin from the Olabisi Onabanjo University (Nigeria), explain how their collaboration led to the production of over 400 pieces of PPE for the local hospital and surrounding community, including those providing essential and frontline services. This included face masks and face shields, at a time when a global shortage meant it was impossible for these to be sourced by traditional companies.
In their collaboration, they leveraged existing open-source designs detailing how to manufacture approved PPE. This allowed Nigerian researchers to source, build and use a 3D printer and begin producing and distributing protective equipment for the local community to use. Plus, it was affordable.
One 3D printer operator and one assembler produced on average one face shield in 1 hour 30 minutes, costing 1,200 Naira (£2.38) and one mask in 3 hours 3 minutes costing 2,000 Naira (£3.97). In comparison, at the time of the project, commercially available face shields cost at least 5,000 Naira (£9.92) and reusable masks cost 10,000 Naira (£19.84).
Dr Maia Chagas, Research Bioengineer at the University of Sussex, said: “Through knowledge sharing, collaboration and technology, we were able to help support a community through a global health crisis.
“I’m really proud of the tangible difference we made at a critical time for this community. As PPE was in such high demand and stocks were low, prices for surgical masks, respirators and surgical gowns hiked, with issues arising around exports and international distribution.
“We quickly realized that alternative means of producing and distributing PPE were required. Free and open-source hardware (FOSH) and 3D printing quickly became a viable option.
“We hope that our international collaboration during the pandemic will inspire other innovators to use technology and share knowledge to help address societal problems, which were typically reliant on funding or support from government or large research institutions.
“With open source designs, knowledge sharing and 3D printing, there is a real opportunity for us to start addressing problems from the ground up, and empower local communities and researchers.”
Dr. Royhaan Folarin, a Neuroscientist and lecturer of anatomical sciences at Olabisi Onabanjo University in Nigeria, said:
“During the pandemic, we saw the successful printing and donation of PPE in the Czech Republic by Prusa Research and it became a goal for me to use the training I had received in previous TReND in Africa workshops to help impact my immediate community in Nigeria.”
The international collaboration came about as a result of the TReND in Africa network, a charity hosted within Sussex which supports scientific capacity building across Africa.
After initial use, testers provided feedback commending the innovativeness, usefulness and aesthetics of the PPE and, while the team’s 3D printer was not built for large-scale serial manufacturing, they identified the possibilities for several 3D printers to run in parallel, to reduce relative production time. During the pandemic, this was successfully demonstrated by the company Prusa Research, which produced and shipped 200,000 CE certified face shields.