This Sussex Life: Lucy Hughes, Product Design graduate. “I challenged myself to find a way of using fish waste”
By: Jacqui Bealing
Last updated: Thursday, 10 October 2019
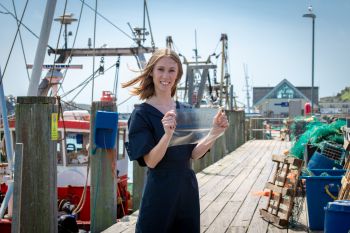
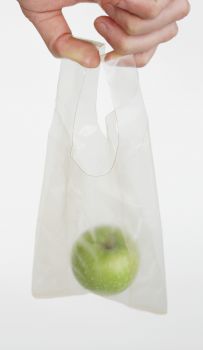
A bag made from MarinaTex
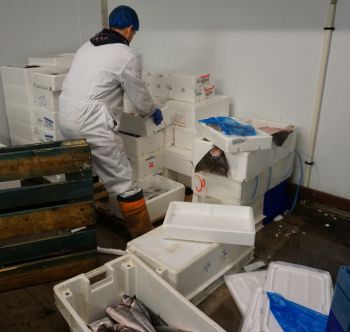
Fish processing in Newhaven
Product design graduate Lucy Hughes has won the UK 2019 James Dyson Award for developing a bioplastic from fish skins that could replace non-biodegradable, single-use plastics.
Initially I applied to do business studies at Sussex. I was doing A-Levels in maths, psychology and design, but I switched to the product design degree course when I realised that all three would complement each other well through design.
I saw Sussex as being a leader in environmental consciousness. In particular, the product design course at Sussex has a circular economy module. The module teaches how we can move from a linear model, in which we take from the earth, make something from it and then dispose of it, to a circular model that is restorative and regenerative by design. What the circular economy module does is close the loop and rethink how we consume, use products and what we waste. In the circular economy, design plays a huge role so it’s imperative this is taught in universities.
I wanted to start with using waste as a resource. One of my tutors had been looking at packaging in the fish processing industry, where there’s a huge polystyrene waste problem, and she got me an invitation to MCB Seafoods Ltd., a Newhaven-based sustainable fish processing plant and wholesaler. They showed me their waste stream of fish skin and scales. In the UK we produce over 492,000 tonnes of fish waste annually.
I was always an avid viewer of BBC’s Blue Planet [which showed the amount of pollution caused by non-biodegradable plastic in the oceans], and I wanted to see if could do something with this plentiful supply of waste. I found out about algae bioplastics, which are made from red algae and form a kind of plastic substitute, so I challenged myself to find a way of using the fish waste with this base formula.
I started by grinding scales with a Nutribullet and pestle and mortar, in my kitchen. Although this did point me in the right direction, I quickly realised this wasn’t the best way of doing it. For three to four months I was running experiments daily, trying to refine the process and formula.
There were a lot of times at the beginning when things were going mouldy and I was wondering what the hell I was doing. My friends and family thought I was crazy. I went between the kitchens in my student home and my family home in London and everyone had to put up with the smell of fish. Even when you store fish in the freezer, because fish are cold blooded, the enzymes are still active, this releases the smell. Sorry guys!
I kept going because I knew that the justification of the project outweighed the end product. If the end product didn’t work out, I’d sleep easier knowing that the motives were solid. But if the reason why I was doing it was flawed then I wouldn’t have had the motivation to continue the project.
I realised that I was part of a movement rather than just a crazy person in a kitchen when I saw an exhibition at the V&A Museum in London called Fashion From Nature. It showed examples of how we have exploited nature, and some new examples of how we are working with it symbiotically. By that point I had a tangible material, but it was great to see other people doing exciting things in fashion with waste products.
Once I had come up with the basic material, I continued to experiment to see if it could be used as a food wrapping, or for other uses, and to see how biodegradable it is. When MarinaTex is in soil at the right temperature it will degrade in four to six weeks, which is faster than many other biodegradables. It’s also economical, one Atlantic cod could generate enough organic waste to produce 1,400 bags of MarinaTex and using a waste material reduces production cost.
It was very exciting to win the UK James Dyson Award, and to see my product entered into the international phase of the competition. The family are really proud, a lot of fish puns have been flying around, but they are all very supportive.My parents approach problem solving in different ways. Dad has always been more detail oriented and Mum has always been more interested in thinking holistically. I can see how I’ve taken a bit from each of them in the way I approach design problems.
When I have a bit more understanding about MarinaTex, I will look at commercialisation. It’s a really exciting time – and a bit terrifying – for me. But I really believe in what I am trying to do, and the positive feedback has been overwhelming so that is a huge motivation.
This profile is part of our This Sussex Life series.